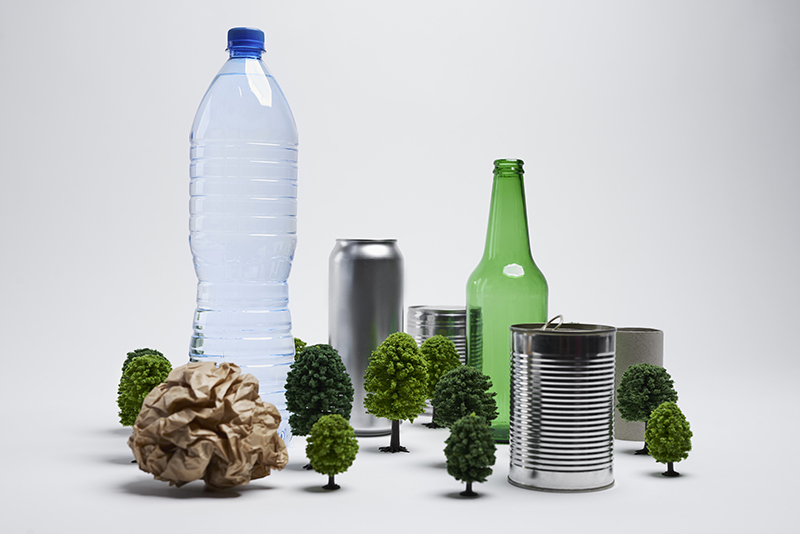
How did we get here?...
The most common type of 3D printer uses FDM technology. This stands for fused deposition modelling where the nozzle of the 3D printer extrudes filament in layers to build up an object.
This technology has been around for longer than you might realise.
They filed the first patent for this type of manufacturing in 1984, and this set the groundwork for 3D printing today.
Despite the introduction of new technologies, FDM hasn’t changed allot in the past decade.
When first invented 3D printing typically used a plastic called ABS. ABS is a thermoplastic heavily used in the injection moulding industry.
The trouble with ABS is that it’s derived from fossil fuels, is not biodegradable, and has a greater environmental impact than other filaments.
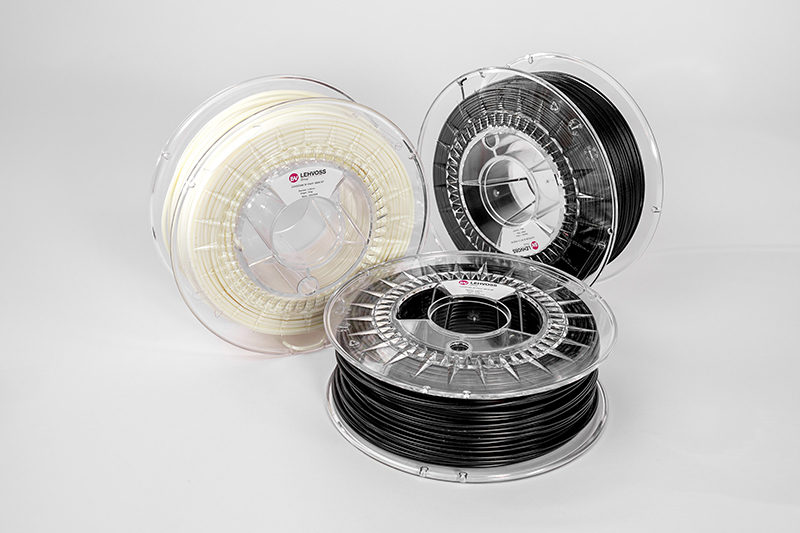